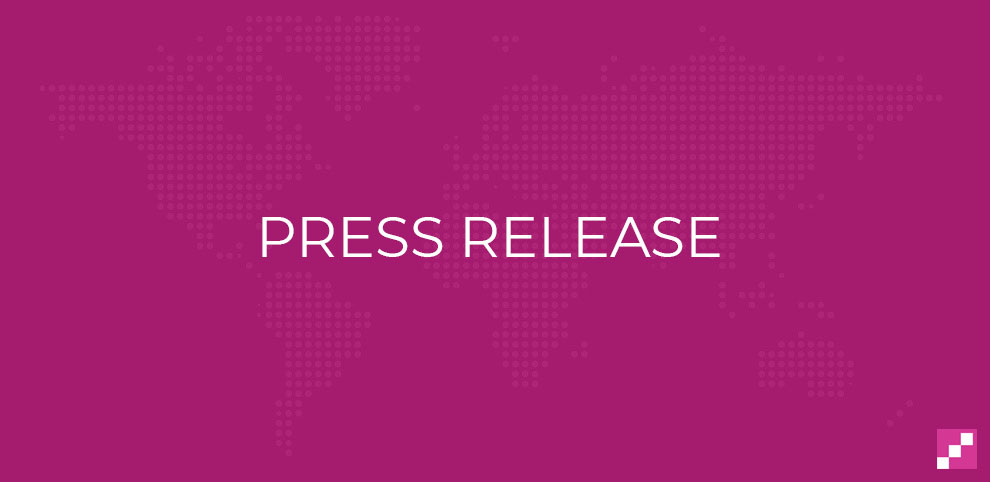
Lockdown Unlocks World First Evolution in Motorcycle Helmet Safety
Published By Pressat [English], Wed, Sep 22, 2021 10:46 AM
While the world was in lockdown limbo, The Helmet Inspection Company went from idea to launch in just 16 weeks, delivering the world’s first non-destructive helmet safety inspection technology.
When Aberdeen-Based businessman, and keen motorcyclist, Martin Slowey dropped his new motorcycle helmet just before lockdown, his question was a simple one: “Is my helmet still safe to use?”.
The answer, however, was not.
After days of searching and emailing, he turned to the internet, hoping that someone might know of a solution. They didn’t. The consensus was that you only had two options: risk it or bin it. Having spent nearly £500 just two weeks previously, Martin was reluctant to risk it but understandably unhappy about the expense of replacing it ‘just in case.’ He wanted to know for sure.
With no solution presenting itself, Martin took action and, The Helmet Inspection Company was born. Now entering its sixth month, this cutting-edge service is attracting attention from public safety, defence and professional motorsport organisations across the UK while continuing to service private motorsports consumer orders through its website portal, where customers can book and track their helmet scan, arrange a door-step collection, shipping or alternatively locate a nearby authorised drop-off centre.
Working with CTO Prof John Tyrer, the UK’s leading expert on laser technologies, The Helmet Inspection Company scientifically determines the integrity of a helmet outer shell using shearography, a laser-based technology used in maritime and aviation to test composite material integrity.
“From dropped and dinged helmets to concerns about age, environment or provenance, there are many reasons that riders have chosen to scan their helmets, but, at the end of the day, it all comes down to one thing: peace of mind.” Said CEO Martin Slowey, “ Our helmets are safety-critical bits of kit. We never get on a bike without them, and yet, while we check our brakes, tyres etc., we tend to choose our helmets based on a range of non-safety criteria and then not give them much thought after that – until something happens! This service allows both for reactive reassurance in the event of potential damage and proactivity for those who want to build a more mindful safety routine.”
With over 1.5 million motorcycle owners in the UK - only 1% of road traffic - motorcyclists account for over 20% of deaths and severe injuries in road traffic accidents. As a growing industry, the number of motorcycles on UK roads increases every year, and with it, the need for quality, reliable safety gear has never been more acute. Yet, while the $700Million premium helmet manufacturing industry continues to blossom year on year, the ability to conduct non-destructive testing has been an unmet challenge – until now.
“According to manufacturing guidelines, most helmets have a shelf-life of around 3-5 years. The natural degradation of EPS lining primarily drives this, but this does not make the outer shell immune to degradation. Cleaning products, temperature changes, impact damage and other environmental factors can erode or weaken the outer shell, and this damage is essentially invisible to the naked eye. Our technology allows our team to closely survey the composite integrity of the outer shell to determine damage or weakening to the structural integrity, which might compromise its ability to do its job in the moments that matter. This level of certainty enables riders to make an informed choice about when they need to replace their helmet”.
And it’s this ability to ‘see the invisible’ that has the market excited.
Unlike metal or plastic, modern composite helmets are designed to spread the energy generated in an impact. They do this by inverse fracturing when impacted, meaning that they fracture inside the helmet outer shell on this underside of the material. This allows the lining to absorb and spread the shock of the impact and limit damage to the riders head. Once the outer shell is compromised, it renders the helmet essentially useless in terms of head protection. Unfortunately, this highly effective design also makes damage invisible to a visual inspection.
The ability of The Helmet Inspection Company to also determine structural degradation and weakening of the composite at point of scan allows riders to be more proactive in considering age, wear and tear on what could arguably be described as the most critical piece of armour.
With support from across the motorcycling industry, the fledgling company has a growing number of collection and drop off points within retail outlets, led by Ducati Manchester Group, and has recently announced a partnership with Bennetts Insurance to offer discounts to their Bike Social Members.
Press release distributed by Media Pigeon on behalf of Pressat, on Sep 22, 2021. For more information subscribe and follow